TECHNOTE
Label Sensor Types and Technologies
There four different label sensor technologies:
- Optical
- Differential Capacitive
- Single-Ended Capacitive
- Ultrasonic
Each label sensor has strengths and weaknesses. Comparing these strengths and weaknesses will determine what’s best for you. This brief overview of each technology will show you the advantages and disavantages of each. It will also provide a simple explanation of how the technology works.
Check the Label Sensor Performance Comparison page for greater detail on how the technologies compare in registration accuracy and speed.
Ultrasonic
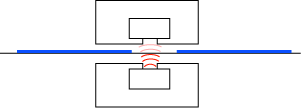
Ultrasonic sensors use high-frequency sound waves to sense the thickness of the web
Ultrasonic sensors measure web thickness with high-frequency sound waves that are transmitted by a transducer under the web to a receiver above the web. More sound energy passes through the web at the gap than during the label. These sensors have no sensitivity to metallic materials and are able to sense labels of almost any material. They can struggle with unique labels that contain multiple layers, especially if there are air bubbles in the material.
Ultrasonic sensors have a great advantage in that they can detect the broadest range of materials. But they are considerably less accurate than capacitive sensors, even at low speeds. Because of the nature of the technology, their accuracy is directly related to web speed – accuracy continually decreases as speed increases.
Capacitive Sensors
Capacitive sensors use electric fields to measure web thickness. The change in thickness between the labels and the gaps triggers the sensor; clear labels are as easy to detect as paper labels. Capacitive sensors come in two configurations: Differential, and Single-Ended. Capacitive sensors are extremely accurate and very fast. They are perfectly accurate at all machine speeds. No other sensor technology can say that.
Capacitive – Single-Ended
Single-Ended capacitive sensors use a single sensing element to measure the thickness of the web. They are adjusted so the liner thickness is below the sensor’s trigger point. The label+liner thickness exceeds the trigger point and the sensor is triggered. If there are any metallic materials on the label, the sensor sees an increase in thickness, but because the measurement is already above the trigger point, it has no affect on the sensor output.
Metals appear very thick to capacitive sensors. If a label is entirely metallic, such as a foil or metallized mylar material, the apparent thickness of the labels may overwhelm the sensor, even at the gap, so that it is unable to detect the gap. Often times, a skilled operator can adjust the sensor to work with solid metal labels, but this may not always be the case.
Capacitive – Differential

A single-ended capacitive sensor has a single sensing element that measures the thickness of the web. Capacitive sensors are so sensitive to metallic materials, that even over the gap, solid foil labels will be seen by the sensing element’s electric field.
Differential capacitive sensors use two capacitive sensing elements to sense web thickness. The output of the two sensing elements are subtracted from each other so that the sensor only has an output when one sensor is over a label and the other is over a gap. The advantage of differential sensing is that small changes in distance between the sensing elements and the baseplate due to temperature shifts or vibration do not affect the sensor.

Differential capacitive sensors use two sensing elements to detect gaps. The sensor only triggers when there is a difference between the two sensing elements.
Metallic materials or inks look very “thick” to capacitive sensors. Because differential sensors trigger on differences of thickness between the two sensing elements, metallic artwork or text can cause the sensor to trigger many times as the artwork passes through the sensor. Differential sensors cannot be used when metallic materials or ink are used on the label or liner.
Optical
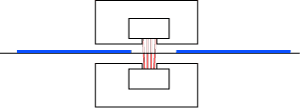
Optical sensors use a beam of light, often infrared, which can penetrate the liner but is blocked by the label material.
Optical sensors use a beam of light, often infrared, which can penetrate the liner but is blocked by the label material.
Optical sensors work by placing a light source (usually infrared) under the web and a detector above the web that measures the brightness of light coming through. Changes in the opacity of the label compared to the liner between labels is used to detect the label edge.
The obvious problem with optical sensors is that they cannot detect transparent or clear labels, regardless of what the liner material is. Clear labels do not block any light, so the edge is not detectable by optical sensors.
Sometimes “eyemarks” are added to the liner – black bars between the labels. The cost of eyemarks is much greater than the cost of a sensor capable of sensing clear labels.
Optical sensors are perfectly accurate at low speeds. At higher speeds, their accuracy degrades a small amount.