Capacitive Sensor TechNote LT03-0022
Copyright Ā© 2013 Lion Precision. www.lionprecision.com
Summary
In some cases, ungrounded targets may affect measurement results. This TechNote examines when ungrounded targets may cause errors and the parameters that determine their magnitude.
Ungrounded Targets with Capacitive Sensing
Synopsis
Most ungrounded targets have a large capacitance to ground. In these instances, there are no measurement errors. This is the case in the great majority of ungrounded target applications. The greatest potential for errors from ungrounded targets is when the target is small or at a significant distance from any other grounded object. Higher-resolution calibrations are more susceptible to these errors than standard or extended-range calibrations.
Symptoms of an ungrounded target
Low sensitivity, decreased standoff, and output vary when the operatorās hand is brought near the measurement area; any of these may indicate a poorly grounded target.
The Role of Ground in capacitive sensing
Capacitive sensing works by measuring the amount of electric current that flows between the probeās
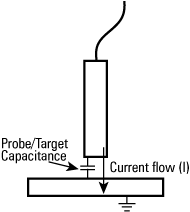
Sensing current flows to the ground through the probe/target capacitance. The amount of capacitance (proximity of the target) determines how much current will flow.
sensing surface and groundāusually the target. The greater the capacitance between the probe and the target (the closer they are), the greater the current flow. The driver electronics are responsible for creating, controlling, and measuring the sensing current.
The mathematical details
I=V/XC, and XC = 1/(2ĻFC)
where:
I = Current
V = Voltage of drive from driver electronics
F = Frequency of drive from driver electronics
C = Capacitance
XC = Capacitive reactance (resistance to current flow)
Capacitive sensors assume that all changes in the sensing current are a result of a change in the probe/target capacitance because of a change in the probe/target
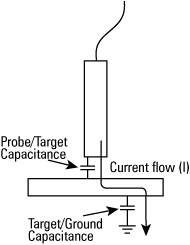
With ungrounded targets, sensing current flows through the probe/target capacitance and then through the target/ground capacitance. If the target/ground capacitance is 100 times (or more) greater than the probe/target capacitance, the measurement is virtually unaffected.
Ungrounded targets
For sensing current to flow, it must find a path to the ground. Anything that changes the resistance to the current flow will affect the measurement. The effect of using an ungrounded target depends on the alternate path the sensing current takes to ground and how much resistance (XC) it encounters along the way.
Capacitive grounding
Many targets, while not directly grounded, have a capacitance to ground. In this case, the sensing current will flow through the probe/target capacitance and then through the target/ground capacitance. If the target/ground capacitance is considerably larger than the probe/target capacitance (>100 times), the total change in resistance to the current flow is negligible and the measurement remains unaffected. If the target/ground capacitance is smaller than this, the measurement will be affected.
Estimating capacitance
Roughly speaking, the capacitance between a probe and the target is about 1pF (picofarad). The approximate capacitance between two parallel plates is:
Metric: C = [8.86 x10-15][Area(mm^2)/Gap(mm)]
Inch: C = [0.225 x10-12][Area(inch^2)/Gap(inch)]
Example: Two 1″ square plates, 0.001″ apart have a capacitance of 225pF.
A typical air-bearing spindle rotor has about 1000pF to ground, making the measurement error essentially zero.
Offset and sensitivity errors
When an error is introduced by an ungrounded target, it comes in two forms:
offset errorāa shift in absolute probe/target distance at zero volts output, and
sensitivity errorāa change in the amount of output voltage change relative to a given change in probe/target distance. Because capacitive measurements are usually relative to some set point as opposed to absolute gap measurements, the offset error is usually of no consequence. The greatest concern is with changes in sensitivity, as this will change the relative measurements made with the system.
Varying target/ground capacitance
If the target/ground capacitance is small enough to generate errors and it varies with time, the variance of the capacitance will appear as time-variant noise on the output. When the capacitance changes, a small DC shift will occur in the output voltage. Continuous changes in the capacitance will create a corresponding continuous change in the output voltage which will appear as noise.
Solutions for ungrounded targets
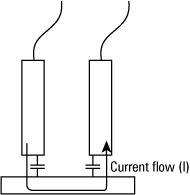
Two-channel measurements can eliminate the need for a grounded target by providing a return path for the sensing current, but only when the two channels are synchronized 180° apart.
Two-channel, out-of-phase measurement
Make measurements with a two-channel system in which two drive channels are synchronized 180° out of phase. In this configuration, the current path is āoutā of one probe, and āinā to the other. Grounding is no longer an issue. A simple gap measurement only requires the output from one channel. The second channel only provides a return path for the sensing current. Some measurements, such as two-channel thickness, can make use of both channels.
Two-channel limitations
The two-channel approach to ungrounded targets requires that the current flow in each channel be identical. Any difference between the two channels will leave a residual charge on the target and create an offset error. Both channels must be the same model probe and electronics and calibrated to the same specifications. Also, the two channels must be synchronized and 180° out of phase. Using two channels not configured accordingly will not be beneficial.
Small phase changes can occur at different points in the probe’s calibration. If one sensor is at its minimum gap and the other at its maximum gap, the phase difference may be enough to reduce the benefits of the two-channel approach to ungrounded targets. If this happens, the target will begin to exhibit behaviors of an ungrounded target when the probes are in this condition.
Grounding with brushes
A grounded piece of flexible conductor can often be used as a ābrushā to maintain a ground connection to an otherwise ungrounded target. Strips of copper or a metal brush will work well for this.
Specific data
The tables below show specific results of ungrounded targets with two different calibrations. Both calibrations are higher resolution calibrations. Higher resolution calibrations hold the probe closer to the target. This increases the probe/target capacitance, which in turn increases the required target/ground capacitance.
Download this video (Right-click > Save Link/Target As):Ā mpgĀ (48M) |Ā mp4Ā (10M)